Changes progress at a blistering pace within today’s real-world construction environment. Technologies, equipment, and processes are continuously evolving within construction projects, making the emphasis upon safety of utmost importance across all disciplines and types of construction.
Job site safety is not a new concept and has long stood as the No. 1 priority of most organizations. Safety managers and teams monitor job-site safety to develop sound safety programs. Equipment managers proactively promote safety through safety meetings, training, and discussions concerning safety risks. Equipment teams and site personnel receive this detailed safety information, obtain proper PPE, and move forward with production activities. These steps and actions are critical in an organization’s safety plan, yet not a single day passes where a serious accident severely injures (or worse) a worker on a construction site.
Risk is inherent with equipment operation and construction activities, yet most accidents involving injury are preventable. When an accident occurs, production comes to a halt, emergency assistance is immediately rendered, and an incident/accident investigation is initiated. The investigation often identifies as a root cause a variance from procedure, an outdated procedure, or a lack of a proper procedure. Looking somewhat deeper, many incidents and injuries occur when adverse actions occur when proper oversight is unavailable or off site.
Read also: Keep tire techs safe
Everyone understands that “the human resource is the most valuable resource.” Collectively, everyone within and associated with the organization has responsibilities to protect the human resource through intense and consistent safety practices. Developing or intensifying a good safety culture throughout all levels of the organization can and will reduce safety risk.
A good safety culture has the potential to enhance the organization’s health and stature within the industry. It requires constant attention to safety data, operational detail, and a collaborative commitment from the board and executive branch, which filters throughout the organization. The objective must be to develop an organizational mindset where everyone does the right things and continuously makes sound decisions, even if such decisions could potentially have a negative effect upon the project timeline or schedule.
A sound safety culture does not just happen with a corporate decision. It is a series of steps and actions developed over time with intense effort. The plan instills safety values, behaviors, and commitment to safety practices that become inherent across the organization. Moving to a safety culture begins with the organization’s management identifying safety as a priority, but its execution depends upon three areas of focus.
- Organizational policies. Develop overarching policies that reinforce a high-level safety culture. Such policies must include—but are not limited to—operator training, qualification, and certification standards; substance abuse training and testing; standards for vehicle operation and driving records; and minimum physical ability standards for all positions. Additional policies should establish hazard communication frequency, incident response procedures, and identify the chain of command levels and their respective safety responsibility and accountability requirements.
- Training and development. A comprehensive safety training and development program is essential to identify and relay hazard communication to all levels of the organization. The goal is for all to understand not only how to recognize hazards, but also how to manage safety with established expectations for adherence. Initial training must address the organization’s safety policies to ensure full awareness and understanding of such policies by everyone. The best safety training programs include hazard communication, current best practices on equipment operation, job site-specific safety and navigation concerns, fall protection, entrapment, impacts, and electrical safety as well as proper use of personal protective gear. New workers should be mentored by others experienced with the worksite operations to acclimate them to the specifics of the environment. Risky actions and behavior must be addressed, demonstrated, and identified as reasons to stop work until corrective measures and actions can be taken.
- Safety management. Safety management, measurement, and accountability identify areas of potential improvement as the culture develops over time. Safety management should be addressed with the same emphasis as unscheduled equipment failures. Incidents of any size or type should be categorized using an ascending scale from minor or yellow cautionary incidents to severe or red incidents. Each level should be measured for accountability and development or refinement of policies, procedures, and training programs for future risk reduction. Having a comprehensive safety program measurement frequency is crucial to the success or failure of a sound safety culture and at minimum performed on a monthly basis.
Everyone is accountable for safety within their immediate space/function and area of responsibility.
Read also: What new traits equipment managers need to succeed
First are the frontline workers working directly in the red zone. This group works daily in direct contact with machines, equipment, and materials capable of severe injury in a split second. At all times they must be aware of their immediate surroundings, who is adjacent, what is overhead, site navigational patterns and movements, and many other potential dangers. They must be impowered to immediately stop any function being performed within their immediate worksite area that they feel may be unsafe. Only until the team lead or others have reviewed the issue, the has been issue corrected, or the situation identified as safe to proceed should the work commence.
Working alongside the frontline workers are the worksite superintendents, project, and construction managers who also are often within the red danger zone. Their area of responsibility encompasses the immediate working area and all adjacent areas and surroundings. Having a larger area of responsibility, they must monitor the activities of supply delivery, subcontractors, and other teams working directly adjacent. Increased communication is the key aspect of safety within this area as well as empowerment to halt activities if a safety concern is detected. A worksite safety representative should be assigned to have authority within this area and at minimum perform a daily safety and production meeting with all workers and production activities on the worksite to minimize risk.
The executive branch of the organization holds safety responsibility for policy and procedure development, training, and enforcement. This level of the organization holds enforcement, measurement, and accountability for the safety program. The executive branch compiles safety and operational data from the operational groups to develop sound safety training programs and policy. The safety manager, or position assigned this responsibility, should be identified within this level of the company, having authority across all functions to implement safety policy, processes, and procedures. Actions initiated and implemented from the executive branch must be collectively reviewed by all various functions to ensure every aspect of the organization is included within the safety culture.
A good safety culture does not begin upon arrival or end upon departure from the worksite. It must become a mindset for all within the organization at all times, on or off the job. All employees should be encouraged to maintain a similar emphasis on safety within their personal lives as well. As important as it is to ensure the safety program has been developed so all can go home to their families at the end of the day, it is equally important they remain safe, and return to their working family and team the following day.
About the Author
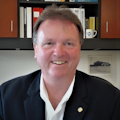
Mike Brennan, CEM
Michael Brennan is a 40-plus-year industry veteran and consultant in vehicle and equipment maintenance management. A three-time recipient of the AEMP Fleet Masters Award, he focuses upon process improvement, facilities management, succession planning, technology, and lifecycle analytics as the cornerstone of success in the equipment management industry.
Read Mike's asset management articles.