Engines in vocational trucks are usually set up to rev higher than their cousins in highway tractors. A greater rev range allows more flexibility for rolling over varying terrain and in rough dirt or mud, and it makes time for the up- and downshifting that might be needed. While cruising, higher rpm keep a dump truck or mixer moving briskly on hills and in stop-and-go traffic.
But many construction-related trucks stay on pavement while hauling building materials and aggregates. They travel on Interstates and freeways, with conditions similar to what freight carriers see, even if trips are shorter. So they can be geared to keep engine revs low, especially at cruising speeds, and obtain better fuel economy.
The latest strategy for highway tractors is “down speeding,” and that’s illustrated here by a Volvo VNL760 sleeper-cab tractor with I-Torque. It’s a working truck but is frequently displayed at trade and truck shows to promote the down-speeding concept. The Volvo belongs to Joel Morrow, an owner-operator who doubles as a consultant to factory engineers, telling them what works and what doesn’t in the real world.
Morrow currently is reporting on his version of I-Torque, which uses a 14-speed I-Shift automated manual transmission; production models are spec’d with a 13-speed, and both use an extra gearbox bolted onto the standard 12-speed I-Shift. In that box are one or two low-end ratios that provide good startability and allow use of an overdrive top gear and, in Morrow’s tractor, a “fast” 2.16 axle ratio.
The system also includes a 455-horsepower Volvo D13-TC diesel. TC means turbo-compounding—a second turbocharger that adds extra power to the engine’s flywheel, so less fuel is needed to maintain rated horsepower and torque.
Volvo I-Torque benefits
I-Torque seemed impressive enough to a group of American and Canadian truck writers that it recently gave it their annual Technology Achievement Award. I chaired the award committee but confess that I hadn’t put I-Torque high on my voting list. This drive was my opportunity to experience its supposed benefits.
I connected with Morrow at the ATA Technology & Maintenance Council trade show earlier this year, and within a few weeks I was seated in his Volvo as we headed out of Delaware, Ohio.
This day he was pulling a van borrowed from Ploger Transportation, where he once worked and which is now owned and operated by his brother, Jerry Morrow. The van carried a load of bottled water, and he figured the rig’s gross combination weight was about 73,000 pounds.
To test the I-Torque I suggested traveling east on State Route 37 through Newark, then southeast on SR 146 to Zanesvillle, and east on Interstate 70. Terrain in eastern Ohio begins rolling as one approaches the Appalachian foothills, presenting some stiff grades to test a tractor’s strength.
As with most VN series tractors, Morrow’s Volvo was comfortable and quiet, so we could converse in normal tones of voice. He is a true believer in the I-Torque concept but explained its operation in a matter-of-fact manner as we proceeded.
“Low engine speed saves fuel because pistons operate slower and pump less air,” he said. “Reducing air flow through the engine means it cools less; everything stays hotter, which makes fuel burn better, and a hot exhaust stream makes the aftertreatment system work better.”
Does that mean fewer regenerations? I asked. “None!” he declared. That’s a good thing because “regens” use extra fuel to burn off soot caught in the diesel particulate filter’s honeycomb structure. Sufficiently high combustion heat alone is enough to eliminate the soot.
Volvo predictive cruise control
A third component of I-Torque is predictive cruise control, which minds a rig’s road speed and anticipates up- and downgrades by ordering changes in throttle settings, transmission ratios, and engine braking. The CC’s control module memorizes the lay of the highway it’s on and, via GPS locating, exactly where each terrain feature is. The next time the truck travels a mapped route, it knows what to do.
For instance, it might order the tranny to downshift just before the rig hits an upgrade, adding power for the climb. Then it cuts the throttle and engages the engine brake on the other side of the hill. Morrow’s Volvo had not been on this route, however, so this feature did not come into play during our drive.
One thing construction-fleet managers—and most truck operators, for that matter—might shun is the tractor’s 6x2 axle layout. The tandem has a single drive axle behind a nonpowered “pusher” axle that’s automatically raised or lowered based on weight and traction required. It’s down under heavy loads but rises a bit to add weight and traction to the drive axle if its wheels slip, and it fully raises when running empty. Volvo calls it Adaptive Loading. Morrow said he’s never suffered from lack of traction.
Morrow used a light foot on both the accelerator and brake pedal, and that contributed to a smooth, quiet, and safe ride. I peered over at the tachometer and saw that it stayed down toward 1,000 rpm, revving to 1,300 or 1,400 before the tranny upshifted. Engine sounds and vibration were muted, contributing to a relaxed and unhurried mood in the cab, even though he kept highway speed at or just above posted limits.
“In a 70-mile-per-hour zone, I run at 72 or 73,” he said later, as we were on westbound Interstate 70. That keeps a rig going with the flow of most other truck traffic and delivers freight to its destination on time. Morrow hauls a lot of high-end furniture made in Norwalk, Ohio, mostly out West and as far as the Pacific Coast.
He talked about the effects of downshifting on engine revs, referring to the I-Shift’s 12th, 13th, and 14th ratios as “underdrive, direct drive, and overdrive.” This is a phrase from the olden days of twin-stick transmissions whose 4-speed back-box ratios carried those labels, along with a “low” or “low-low” designation for the start-out gear. Drivers of yore stayed busy shifting through setups like that, but an automated gearbox like Volvo’s does all that work by itself.
I took the wheel just before we reached the SR 37/161 freeway west of Newark. High winds had been predicted, and they picked up as a weather front flowed through the region. The turbulent air buffeted the van and our cab, and I made constant steering corrections to keep the rig in our lane. This tractor had Volvo’s Dynamic Steering, with an electric motor adding assistance to the hydraulic system. But controlling the rig was still a chore.
I watched the tach as I slowed to 50 and 55 mph while the freeway wound through Newark and saw that the needle swung to 1,400 and sometimes 1,500 rpm if I put my foot into it a bit, then fell back toward 1,000 while cruising, as when Morrow was driving. There was only a bit of vibration at low revs.
I asked Morrow about fuel economy with his I-Torqued Volvo.
“I’m averaging 10.1 miles per gallon right now,” he said, and most of those are loaded miles. “On one run, running empty on a calm day, east out of Denver, I actually got 15 mpg. The least I’ve seen is 6.53, and that was in a snowstorm, stuck in traffic, stop-and-go.” Down-speeding makes sense and saves dollars, and might have a place where there’s a lot of steady-speed running. I reckon it deserves that award we gave.
About the Author
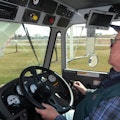
Tom Berg
Tom Berg is widely acknowleged as one of the top truck writers in the industry. He has covered construction for more than 34 years, and has test-driven well over 150 trucks for Construction Equipment.