Renew the attack on unscheduled failures
The evolution of maintenance management brings with it challenges to some long-standing fundamental aspects of effective equipment management. Lingering pandemic concerns, including a potentially long-term supply chain crisis, have coupled with a scarcity of qualified technicians and operators, plus looming recessionary fears. Executives are reviewing all fundamental equipment functions and metrics to find efficiencies and overcome this new set of challenges.
Disruptions in the supply chain challenge just-in-time’s effectiveness for acquiring parts and supplies in a timely manner, making it difficult to schedule preventive and predictive maintenance repairs and actions.
Proactive equipment managers understand that all aspects of equipment maintenance must concentrate upon the reduction or elimination of unscheduled equipment failures, most importantly red events within priority “1” primary or critical machines that may threaten project production schedules. To accomplish this, they have established sound preventive/predictive/condition-based maintenance programs developed around industry best practices. These organizations have recorded an elevated level of success in maintaining a much higher percentage of scheduled maintenance compared to unscheduled maintenance and repair work.
The post-pandemic era has brought to light a new set of challenges that have increased unscheduled failures and maintenance. To address these challenges, managers need to examine the impacts of technological advancement, equipment idled during the pandemic period, supply chain disruptions, qualified labor, and operational compliance. These challenges have recently created a constant sense of urgency, frustration, and, in some cases, crisis management within the equipment function.
Examining these areas and refining a strategy to increase the ratio of scheduled versus unscheduled maintenance and repairs should be at the forefront of equipment managers’ initiatives.
Scheduled vs. unscheduled
Scheduled maintenance includes proactive prevention measures such as operator care, preventive maintenance, scheduled inspections, and specific component repair/replace actions. It remains the most cost-effective option to reduce the percentage of unscheduled maintenance failures.
Unscheduled maintenance and repair occurs when major components are run beyond their designed operational limits, ultimately failing, and require immediate repair before the machine can be returned to service. Exceeding operational limits can be caused by lack of maintenance or operator care, misuse, and the application of an undersized machine, to name a few. Unforeseen component failures often result in excessive cost, downtime, and scheduling delays.
Asset managers have seen many technological advances over the past decade. Telematics, advanced maintenance information systems, and fuel- and project-management system integrations provide equipment managers with an abundance of data. To reduce unscheduled failures, managers must define the volume of available data required and ensure data integrity of all associated specific systems.
Equipment managers must understand that there is far more data available than required for a successful and proactive maintenance strategy. They should define and access only the specific data sets, or “useable data,” required for effective maintenance and scheduling. These actions will enhance scheduling effort, timeliness, and completion of scheduled work, thereby reducing unscheduled failures.
Independent systems application data that has been integrated for effective equipment management is often manually loaded and updated for each specific application. This task is assigned to a specific function of the organization, or multiple organizations, and is subject to input error. Review data integrity and automate the specific systems’ data entry processes to eliminate erroneous data entry. In doing so, effective scheduling of high-priority machines and repairs will increase.
Equipment idled for prolonged periods of time often prove unreliable when re-deployed to full operational capacity. Excessive failure ratios to primary and secondary systems and components due to inactivity are common with idled equipment. Fleets that idled equipment for prolonged periods during the pandemic shutdown are now experiencing increased failures as it returns to service, significantly increasing the volume of unscheduled repairs.
Prior to re-deployment, a detailed condition assessment must be completed. Address all identified defects prior to dispatch to minimize this type of unscheduled failure.
Supply chain disruptions are a significant threat to proactive scheduled equipment maintenance. For better than a decade, most organizations with in-house maintenance functions employed a just-in-time supply operation. Parts and supplies were readily or reasonably quickly available from OEMs and several other suppliers, which allowed consistent order/delivery times while minimizing inventory cost. Ensuring part availability to meet maintenance scheduling parameters was simple and dependable.
Current disruptions in the supply chain have significantly challenged just-in-time’s effectiveness for acquiring parts and supplies in a timely manner. It is a significant challenge to schedule preventive and predictive maintenance repairs and actions. Such supply chain disruptions have upended order and delivery times and availability, forcing machines out of service for extended periods. In response, equipment managers must deploy a second machine at significant and unrecoverable cost to maintain the project schedule.
To improve part and supply availability, organizations must expand their primary, secondary, and third-source networks. Web-based sourcing should be expanded, and order/fill rates should be documented to identify high-performing suppliers and their consistency.
Machine downtime due to parts availability should be documented. Parts having unacceptable lead times should be identified for potential inventory increases.
Inventory levels should be reviewed. Increase the levels of high-volume, low-cost parts in order to meet future demand, and evaluate levels for specialized parts with long lead times.
Increasing part availability and fill rates increases scheduling effectiveness, reducing unscheduled failures.
The availability of qualified labor has a significant effect on reducing unscheduled failures. Vast technical capabilities, extensive knowledge, and continuous training are required for a technician to reach independence and ascend from an apprentice level to a journeyman level. Additionally, technology has allowed technicians on the shop floor and in the field to generate work orders and additional repairs. Along with this authority comes the responsibility to ensure correct documentation of scheduled and unscheduled repairs.
Increased training on preventive maintenance inspection and defect identification and correction is imperative to reduce unscheduled failures. Emphasize proper documentation of scheduled and unnscheduled work. Such documentation provides equipment managers insight on advancing the preventive maintenance plan to reduce future unscheduled failures through proactive maintenance inspections.
Similarly, equipment operators must be trained on all operational facets of the machines they operate. Often operators will know of and simply “live with” an impending defect that over time degrades the component or system to the point of failure or shutdown. Operators are the first line of defense in reducing unscheduled failures. Highly trained and experienced operators can detect subtle changes in machine operation or capability, bringing early notification to maintenance teams for inspection and corrective actions, reducing the possibility of an unscheduled failure.
It is imperative that personnel are fully trained and are timely in reporting potential defects. Intermittent defects reported are often hard to detect by the maintenance team, and in these situations an operator interview should be undertaken to clarify the concerns.
Scheduled inspection compliance is another area of concentration as additional schedule notification may be required by project-management teams to allow for adequate scheduling of machine service. Failure to adequately notify often results in delayed maintenance, which increases technician time and prevents full schedule compliance.
Maintenance managers should eliminate process flaws, increase supplier networks, and provide detailed training, then continuously monitor, measure, and advance these areas to improve machine reliability and reduce unscheduled failures.
About the Author
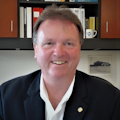
Mike Brennan, CEM
Michael Brennan is a 40-plus-year industry veteran and consultant in vehicle and equipment maintenance management. A three-time recipient of the AEMP Fleet Masters Award, he focuses upon process improvement, facilities management, succession planning, technology, and lifecycle analytics as the cornerstone of success in the equipment management industry.
Read Mike's asset management articles.