You cannot maintain the equipment of today with the tools, technologies and mindsets of yesterday.
The old rope shovel in the picture burned almost anything for fuel, oil was black and dirty, and water was all you needed for a coolant. Preventive maintenance was all but nonexistent, and any day without some sort of mechanical failure was a good day. Fluids were of no concern: Anything would do as long as it was reasonably clean and in the right place. Maintenance was easy, and anyone could do it.
A cursory glance at the pages of this magazine will show you that the world is different. Equipment is better, faster, more complex, and more productive. Gone are the days when smoke coming out of the smoke stack was seen as a sign of solid hard work. Gone are the days when maintenance was a low-tech job performed by an “oiler.” Gone are the days when fuel, oil and water were simple, cheap, low-tech products that required little or no care and attention. Machines of today are much less forgiving when it comes to maintenance.
Let’s look at what has happened to the fluids we use to power, lubricate and cool our machines, and then consider the possibility of defining fluids management as a specialized highly focused job.
Fuel. The transition to ultra low-sulphur diesel (ULSD) in order to lower emissions and improve exhaust aftertreatment has not been without problems. ULSD has a lower lubricity, a lower solvency, a higher wax content, and is more susceptible to micro-organism growth. This increases the need for additives in fuel, decreases the fuel’s ability to dissolve injector and other deposits, and shortens filter life due to micro-organism contamination. These factors combined with the extremely tight tolerances needed in injectors that work at pressures as high as 29,000 psi place a high demand on fuel specification, cleanliness and storage. Diesel is no longer a simple product of the oil-refining process. It is a complex fluid that cools, lubricates and cleans the injection system and provides power to the engine with minimum environmental impact. Volatility in the market, price fluctuations, and starkly different procurement options add to the complexity of the situation. It is no longer a matter of buying a couple of thousand gallons of the nearest and cheapest and filling up your tanks.
Oil
Oils—the base materials from which they are made and the additive packages they contain—are extremely complex, carefully designed fluids. All requirements, lubricity, operating temperatures, and oxidation resistance are up, and oil change intervals are continuously increasing based on improvements in oils, filtration and cooling. Design and manufacturing changes have resulted in a staggering increase in the need for cleanliness. We no longer discuss or debate the fact that cleanliness is “good.” We measure it by ISO standards and we have the knowledge needed to quantify the impact of improved cleanliness on component life. We know that we can reduce the cost of major component replacement for a mid-size loader by 30 percent if we do nothing more than increase oil cleanliness from ISO code 18/15 to ISO code 15/12. It is not a matter of debate or a matter of good practice. It is a matter of hard economics. Storage and filtration are critical at every step in the process. A competent oil-analysis program is no longer a luxury or an option.
Coolant
Coolant is the forgotten fluid. Summer and winter demands vary, and there is a lot of chemistry going on between the fluid and complex metals in the cooling system. Liner cavitation and aluminum corrosion can become major problems if additives and concentrations are not properly measured and managed. As with fuel, it is no longer a question of finding the cheapest and most convenient—water—and topping off the radiator.
Air
It is a fluid, and performance and life depend upon the cleanliness of the air drawn into the engine. The volume of air used is hard to imagine: An average heavy-duty engine requires between 13,000 and 20,000 liters of air to burn one liter of fuel. The filtration system has just one opportunity to filter dust, smog and other particles out of the intake air. Once dirt penetrates any hole, crack or gap in the filtration system, the contaminants are in place to cause damage to all engine components. Tighter tolerances and higher temperatures and pressures increase the demand for filtration, and the need for carefully balanced fuel/air mixtures at all power settings reduces the allowable pressure drops. Ensuring the required quantity and quality of air to the engine is not as simple as it once was.
Diesel Exhaust Fluid
Diesel exhaust fluid (DEF) is a new fluid and is causing a lot of people concern. It is a mix of 32.5 percent high-purity urea and 67.5 percent deionized water. It is sprayed into the exhaust system where it serves as the reactant in the selective catalytic reduction system needed to lower nitrous oxide emissions. Consumption runs at approximately 2 percent of fuel consumption. It sounds simple, and substantial work has been done to make storage and distribution as efficient as possible. It is, however, corrosive to copper and brass as well as other materials. Stringent requirements guide cleanliness, temperature and storage—especially in cold or very hot regions. It is, without doubt, another complex fluid to purchase, store, dispense and manage.
Clearly the world is more complex for all five of these principal fluid types. They are also more expensive, and opportunities for cost reduction through astute fluids management have never been higher. Fuel itself accounts for about one-third of the total cost of owning and operating a heavy-equipment fleet. The other two major cost categories—owning costs and repair and maintenance costs—receive a lot of attention, yet fuel is frequently delivered to the job site and used as and when needed. Unit-level fuel consumption and fuel-cost statistics are rare, and many equipment managers simply shrug their shoulders and say, “There is nothing we can do.”
I beg to differ.
We have the technologies to measure and manage fuel costs with the same care and attention we give to repair and maintenance costs. We do not put technicians and parts on site with no mechanism to keep track of cost and performance, but we often spend more on fuel than we do on parts and labor. We know that all sorts of contaminants get into the fuel, yet we seldom measure quality and cleanliness as it goes into the machine. Substantial improvements have been made when it comes to oil cleanliness. Yet I still see top-off containers exposed to dust and grit, and I seldom come across a full understanding of the savings that can be achieved by improving fluid cleanliness and extending component life. Coolant and air filtration problems persist, and one can only imagine the costs that could flow from a badly managed DEF storage and distribution program.
We have individuals who focus on repairs and maintenance and on running shops and yards. Their knowledge and expertise in these areas pay dividends, and we value their contribution to the organization. Let’s create a Fluids Czar who has a laser focus on the cost savings and benefits that can be achieved from the proper management of the fluids that are the life blood of a productive, reliable and cost-effective fleet. Fluids management has passed beyond the stage where it can be the part-time responsibility of several individuals who just happen to be available or close to the problem. It is a specialized area of expertise, it influences and directly impacts a third of the total cost of owning and operating the fleet, and it can massively impact the reliability and repair costs of every machine you operate.
It is not difficult to write the job description. It is not difficult to justify the investment. Machines are increasingly fluid-intensive, and fuel is increasingly expensive. The need grows with every day.
You cannot maintain the equipment of today with the tools, technologies and mindsets of yesterday. A first step is to change your mindset with regard to fluids and fluid management and cause it to be an area of specialized expertise.
About the Author
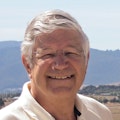
Mike Vorster
Mike Vorster is the David H. Burrows Professor Emeritus of Construction Engineering at Virginia Tech and is the author of “Construction Equipment Economics,” a handbook on the management of construction equipment fleets. Mike serves as a consultant in the area of fleet management and organizational development, and his column has been recognized for editorial excellence by the American Society of Business Publication Editors.
Read Mike’s asset management articles.