Sponsored blog.
Sometimes small changes can make a big difference in the productivity of your machines. For example, a recent “minor” development in some grade control systems eliminates the need for dozer operators to stop production in order to tune the automatic blade control performance. Sounds like a small thing, but good operators want to “hit it and get it” when they get on-site and start pushing dirt.
With almost all grade control systems, operators have to test and tune for how the dozer responds to the type of material they are grading by making a “test” pass... and then make the pass again once they get tuned in. Plus, in many cases they need to stop the machine and re-calibrate the valves when the materials they are grading change... like going from gravel to topsoil.
Today, manufacturers are working on improvements to grade control that reduce or eliminate the need to make a “test” pass. Trimble’s system uses a feature called GradeMax, that has improved algorithms to increase the dozer performance without the cost of additional inertial sensors. Optimizing the valve and blade controls enhances real-time control and accuracy, reducing the need for the “test” pass. Plus, the data update rates are doubled... which increases smoothness for all the grading tasks. The higher update rates and better valve control allow the operator to grade a faster, more consistent run with tighter accuracy.
So, basically, the operator can just start working, and follow input on the controller to fine tune while pushing dirt. Just drop the blade, hit the automatic blade control and fly... for a much more productive result!
Talk to your technology dealer to see if they have a similar feature available. Like I said, it’s a small change, but a big improvement.
You can read many stories about why and how customers made the decision to implement technology, and what their experience has been, at trimble-productivity.com.
About the Author
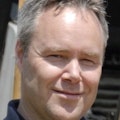
Johan Smet
Johan Smet is Director of Technology Consulting and Services for Trimble’s Heavy Civil Construction Division. He joined Trimble in 2004 as Director for the Construction Division. Johan holds an Engineering degree from the University of Antwerp, Belgium, and an MBA from the University of California, Berkeley.